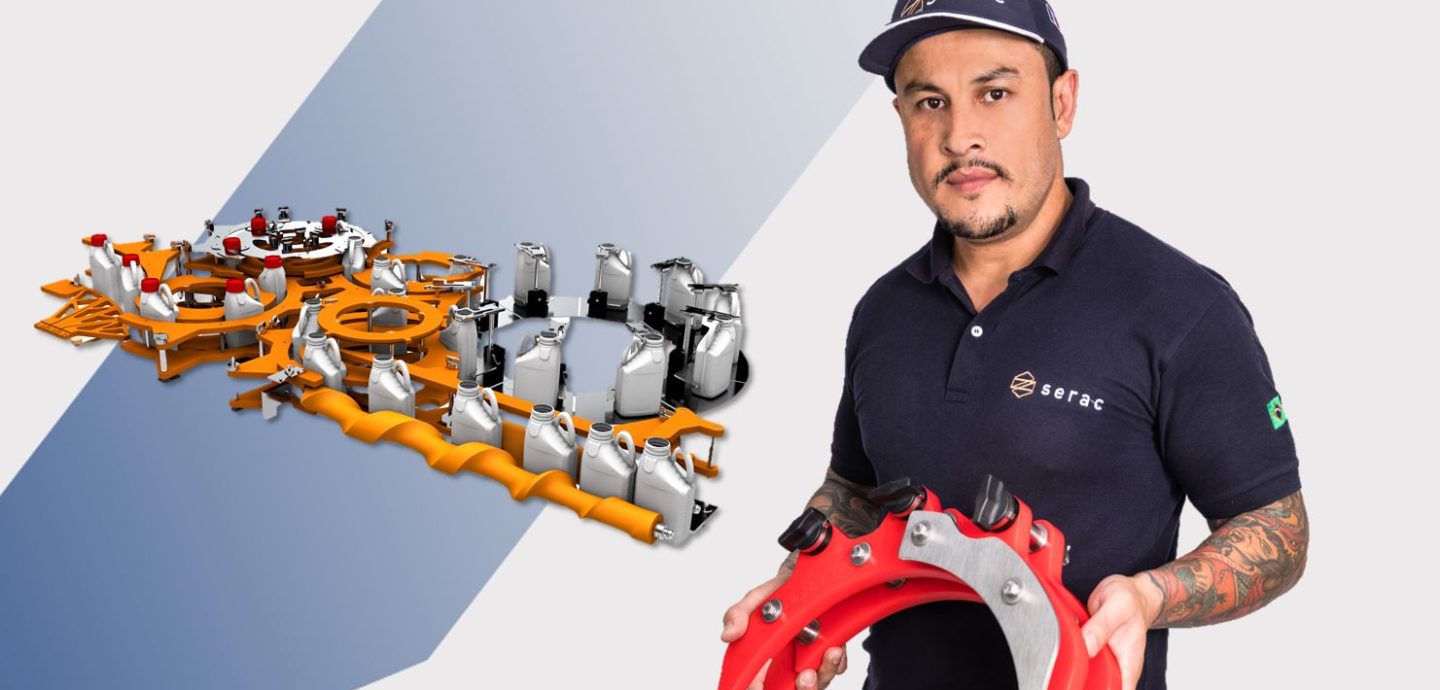
In the packaging industry, bringing new formats into production can be a real challenge. While the initial appeal of a low-cost local tooling supplier may seem attractive, experience shows that working with the manufacturer of your filling and capping machine is the most cost-effective solution in the medium to long term.

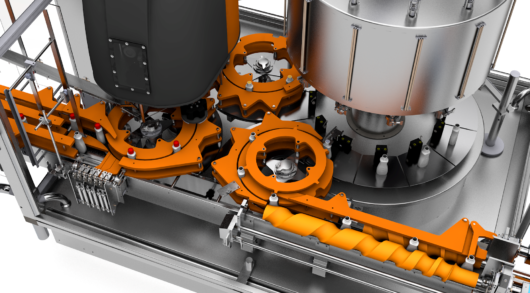
1. Expertise and in-depth knowledge
The manufacturer of your machine has in-depth knowledge of your machine and the setting values required to guarantee a smooth start-up in production. Unlike a standard service provider, the builder can fine-tune tooling to suit the specific features of your equipment. Simulations carried out by the manufacturer enable the correct positioning levels of tooling parts to be defined, guaranteeing bottle integrity, good functionality of the filling and capping processes, and ultimately, the quality of the finished product.
2. Reduced risks and costs
Using a standard supplier can often entail costs associated with quality problems, last-minute adjustments and production delays. The manufacturer, on the other hand, thanks to his specific technical expertise, can prevent many problems before they even arise. This significantly reduces the risk of financial loss and stress, turning the potentially higher initial investment into substantial savings over the long term.
3. Optimized productivity and efficiency
The manufacturer’s technicians are able to optimize machine settings and adjustments, improving efficiency and productivity throughout the production chain. Precise settings and adjustments by experts also reduce operator training time and the risk of errors or non-conformities, contributing to greater profitability.
4. Adapting to industry trends
In a context where the weight and complexity of packaging is evolving rapidly, the manufacturer, thanks to its 3D simulations and advanced knowledge, can guarantee that tooling is not only adapted to current requirements, but also flexible in the face of future changes. This enables better quality management and faster adaptation to new market requirements or regulatory changes.
5. Guaranteed compatibility and support
Choosing your machine manufacturer guarantees perfect tooling compatibility with your existing equipment. What’s more, ongoing technical support and access to original spare parts can significantly reduce downtime and maintenance costs.
Lightweight and/or complex-shaped packaging can be damaged by generic tooling that is poorly adapted to your machine. Relying on 2D drawings or 3D files is not enough to ensure quality circulation.
Digitizing will enable you to identify the hard points on your bottles and measure their top-load, to ensure that the packs are gripped correctly and closed smoothly. All these analyses will lead to the choice of a suitable anti-torque and the fine-tuning of your capping turret.
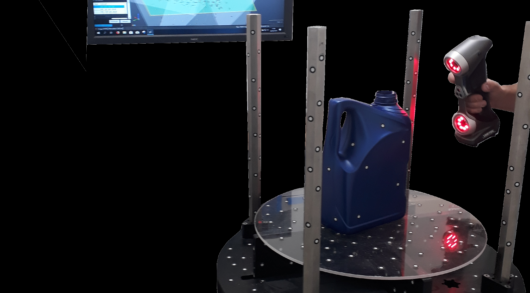
Digitization of empty and full packs
All your packaging needs to be scanned, both empty and full, to identify any deformations and their disparities.
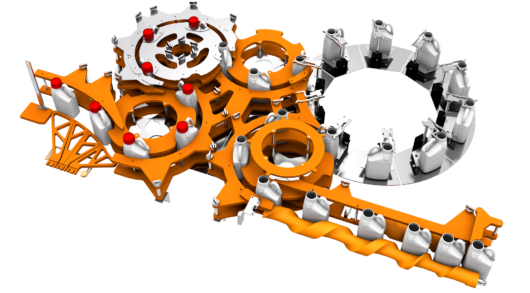
Simulation of packaging circulation
Simulation of packaging circulation in 3D motion ensures smooth circulation that respects your packaging.
Our advice
“ When setting up a new formats project, you need to consider not only the technical skills of your tooling supplier, but also his knowledge of your production line. “
Need new tooling?
Contact our team today to find out how our customized solutions can optimize your costs
and increase your long-term efficiency.